Given the increasingly restrictive limits imposed by the International Maritime Organization (IMO) for the regulation of pollutant emissions in the maritime field, the study of environmentally friendly combined systems for the generation of electricity and heat on board ships acquires increasing importance. The application of combined cycle technology, which permits reaching high efficiency levels, in combination with the use of a clean fuel such as LNG, would give a substantial contribution in the reduction of pollutant emissions. Today, gas turbine based combined plants, widely used in the field of electricity production, thanks to the possibility of achieving, efficiencies up to 60% in large plants [1], are still limited in the naval sector. Most ships use diesel engines due to lower fuel costs, with the possibility of using heavy fuels (such as HFO), which are cheaper but highly polluting. With the tightening of regulations and the consequent need for use of cleaner fuels such as LNG, the focus can shift to the adoption of gas turbines for the topping cycle to be combined with steam turbines for the bottoming cycle. In this combined cycle configuration, the high temperature (500-600 °C) gas turbine exhaust flow may be used in HRSG to produce steam, to be employed to fulfil vessel thermal requirements as well as to produce further electrical energy in the steam turbine. In marine industry notation, the combined gas/steam cycles, with the propulsion units coupled to electric motors, are usually referred to as COGES plants. Although the gas turbine in the naval field has found application mainly in the navy, in the last years it is starting to be considered also for commercial vessels such as fast ferries and cruise ships [2]. COGES plants were first adopted on the Millennium cruise ship [3], but it is a unique case of propulsion system related with the highest efficiency [1]. It can be expected that in the coming years this technology will find a wider development for other vessel categories, given the advantages associated with the use of gas turbines. Indeed, gas turbine are characterized by high power-to-weight ratios, are compact and light, as demonstrated by their almost exclusive use in aeronautics, and offer the opportunity of working with clean fuels such as LNG. The use of LNG for the feeding of gas turbines allows the substantial elimination of sulphur oxides (SOx) and particulate emissions, as well as a strong reduction in UHC and nitrogen oxides (NOx) emissions. Added to this is the fact that thanks to the high efficiencies achievable with the combined cycle configuration, and the consequent fuel consumption reduction, carbon dioxide (CO2) emissions are reduced also due to the low content of carbon atoms present in methane of which LNG is predominantly composed. Given the benefits listed above, a number of works concerning the design and optimization of COGES systems, for large naval applications can be found in literature. Haglind [4-6], in his three-part paper, presents a thorough review on the use of gas and steam combined cycles as prime movers for large ships, highlighting how previous experience for large vessels shows that combined cycles weigh less and require a smaller volume and less auxiliary machines than diesel engines. However, this technology is mature for large plants, but not for smaller engines. The gas and steam turbines can be scaled down, decreasing the dimensions and increasing the rotational speed, but beyond a certain limit, where the aerodynamic losses, as well as the problems related to rotor dynamics, are no longer acceptable, it is necessary to consider a different architecture, which can increase the compactness of the engine. In the case of gas turbines, for example, we should move from the use of axial machines to radial compressors and turbines, which allow obtaining more compact machines, more suitable for the smaller air mass flow rate. Therefore, a completely new design for turbomachinery and the whole system should be considered. As far as mini combined cycles are concerned, very few studies can be found in literature. Salvini et al. [7] have shown that small-scale cogeneration plants based on gas turbines in the 1-6 MWe range can allow significant cost savings, while for smaller sizes the effectiveness of the investment should be carefully controlled. Brostmeyer [8], in his patent describes a mini combined cycle, capable of producing affordable electricity at about USD 1,500 per kW, providing 5.5 MW of electricity plus 3.8 MW of heat. A small gas-steam combined cycle could be used in different sectors in the naval field, both as a prime engine (in the case of ships with low electrical and thermal power requirements), or combined with other engines or in modular configurations for application on larger vessels. The present work is aimed at designing a mini combined cycle (of a size of 2 MW) for the production of both electrical and thermal power for the naval field application. Once the cycle has been defined, the design of the single turbomachines is presented. The component design is aimed at combining the fluid-dynamic requirements with a compact and light-weight design, as well as robustness and low-cost of the product. The mini combined cycle presented here may find application not only on-board vessels, but also for land or off-shore installations.
In Figure 1 the proposed plant scheme is shown. It is a small combined-cycle plant, composed of a micro gas turbine, fuelled by LNG, and a bottoming steam plant, which in turn consists of single pressure HRSG and a steam turbine of small power.
Schematic representation of the combined heat and power system and thermodynamic representation on T-s plane
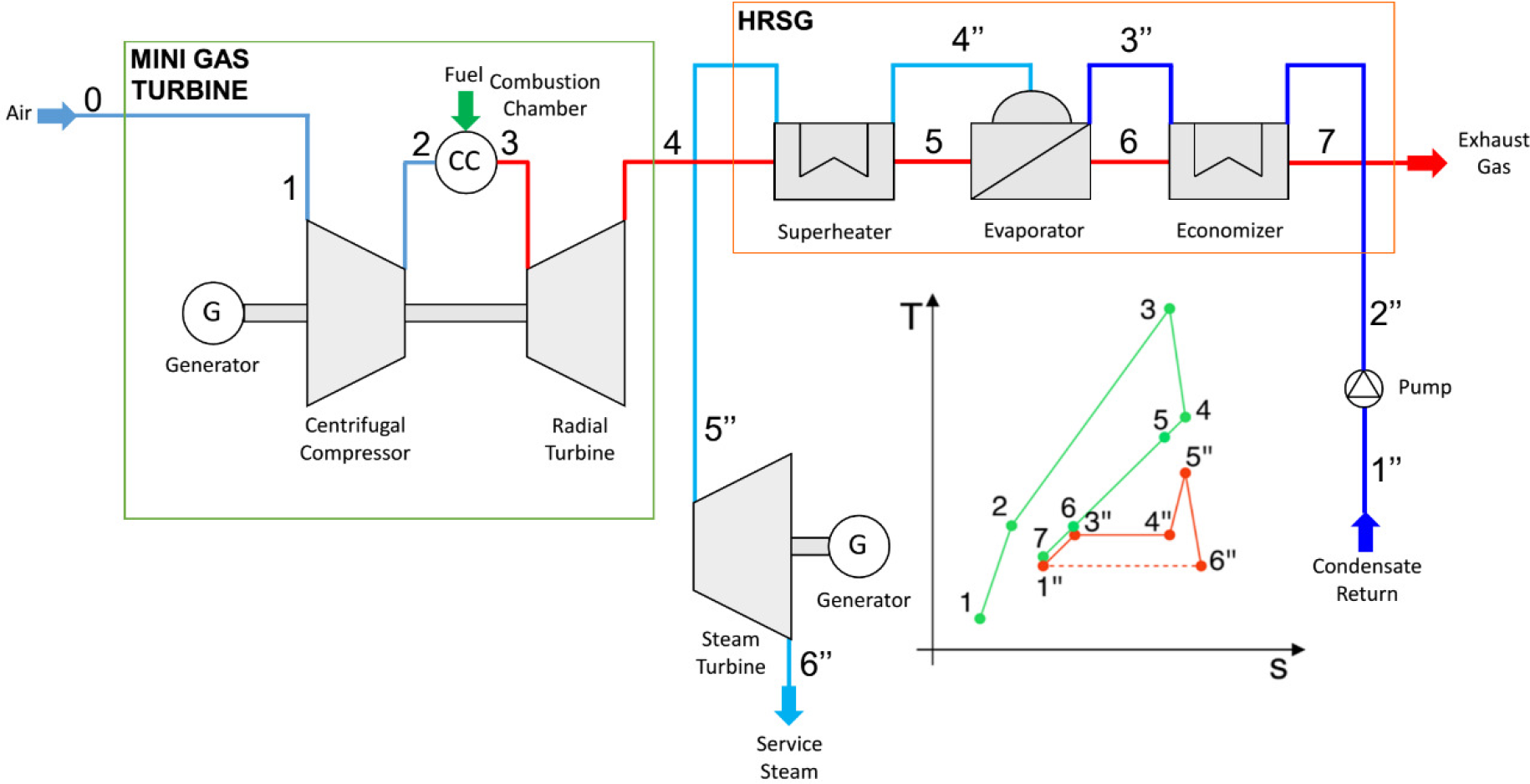
The representation on the thermodynamic plane T-s is shown in Figure 1 where the simple Brayton cycle of the gas turbine and the Hirn cycle relative to the steam plant are represented. The mini gas turbine, in order to reduce the dimensions and costs, consists of a centrifugal compressor, which takes air from the environment and compresses it, a combustion chamber fuelled by LNG, and a centripetal turbine. The exhaust gases from the turbine, being still at high temperature, are used for the production of superheated steam inside a single pressure level HRSG, consisting of an economizer, an evaporator and a superheater, before being released to the chimney. This steam is expanded within the steam turbine, which then takes part in the electrical energy production of the plant, down to a pressure of 3 bar. The steam leaving the steam turbine feeds the steam network of the ship, which therefore satisfies, depending on the thermal utilities considered, part or the entire requirement of heat. The useful thermal power generated by the plant, indicated by H, and used to evaluate the global efficiency of electrical and thermal power, is that associated with the transformation of cooling and condensation at constant pressure of the superheated steam from the turbine outlet to the saturated liquid condition. As mentioned before, one of the fundamental characteristics of the system is that of presenting a high compactness, in order to reduce the volume occupied by the power generating system, consequently increasing the ship payload. However, since the goal is to achieve a combined power and heat generation system, it is necessary to guarantee:
A high electrical efficiency;
A high cogeneration efficiency;
A sufficient production of low pressure steam (3 bar absolute) to satisfy the demands of the thermal utilities on board the ship.
The simultaneous achievement of these objectives for an electrical power plant equal to that required by the applications in question, in particular for a power of about 2 MW, is not obvious [7]. Indeed, it is necessary to respect the constraints imposed by the technologies of the machines and components of the plant. The variables that can be modified for the purpose of achieving the optimum balance between the different targets are the pressure ratio of the simple Brayton cycle and the thermodynamic state reached at the end of the vaporization and superheating process performed by HRSG, that means, on the thermodynamic plane, the value of the enthalpy, or better, of the temperature and pressure at the point indicated by 5’’ in Figure 1.
The performance of the combined cycle was evaluated through the GE GateCycle® simulation software [9]. The three previously mentioned variable parameters (pressure ratio and thermodynamic conditions at the entrance of the steam turbine) were changed within the admitted ranges to the aim of identifying a good compromise between the need to obtain a good electrical efficiency and a good cogeneration efficiency, which are obviously targets in contrast to each other.
The technical limit of the pressure ratio value, indicated with β, above which it is difficult to realize a single-stage centrifugal compressor of good overall performance, is about 6. Starting from this upper limit value, the effect of its decrease is investigated.
As this parameter decreases, on the one hand a lowering of the electrical efficiency of the system occurs, but at the same time an increase in cogeneration efficiency is obtained, as indicated in Figure 2a, due to the increase in the temperature of gas turbine outlet (T4), as shown in Figure 2b. Therefore, if the pressure ratio decreases, in order to produce a certain steam flow rate, fixed by the steam turbine requirements, a lower gas turbine exhaust gases mass flow rate will be necessary, which in turn reduces the size of the top cycle machines (compressor and gas turbine). Finally, in Figure 2c, the influence of the pressure ratio is shown both on the coefficient of distribution of the electric power between the steam turbine and gas turbine (ψ), the overall electric power being fixed, and on the mass flow of the actual exhaust (Φ), but also on the electrical/thermal power ratio (E/H). The maximum admissible values of pressure and temperature at steam turbine inlet section, indicated respectively with p5'' and T5'', are determined by the construction characteristics of the turbine itself. The influence of these parameters on power plant performance is investigated in Figure 3 and Figure 4. When the pressure and temperature decrease, the electrical efficiency of the system decreases (Figure 3a and Figure 4a), while the efficiency of cogeneration increases. This effect is due to the increase in the steam mass flow rate generated within HRSG, in the case of temperature T5'' decrease (increase made evident by the observation of the variation of the parameter ΦS, presented in Figure 3c), and to the increase in the temperature T6'', at the steam turbine outlet section, in the case of pressure decrease (Figure 4b).
Influence of the pressure ratio β on: electrical efficiency and cogeneration efficiency (a), gas turbine outlet temperature (b) and Ψ, Φ and E/H (c)
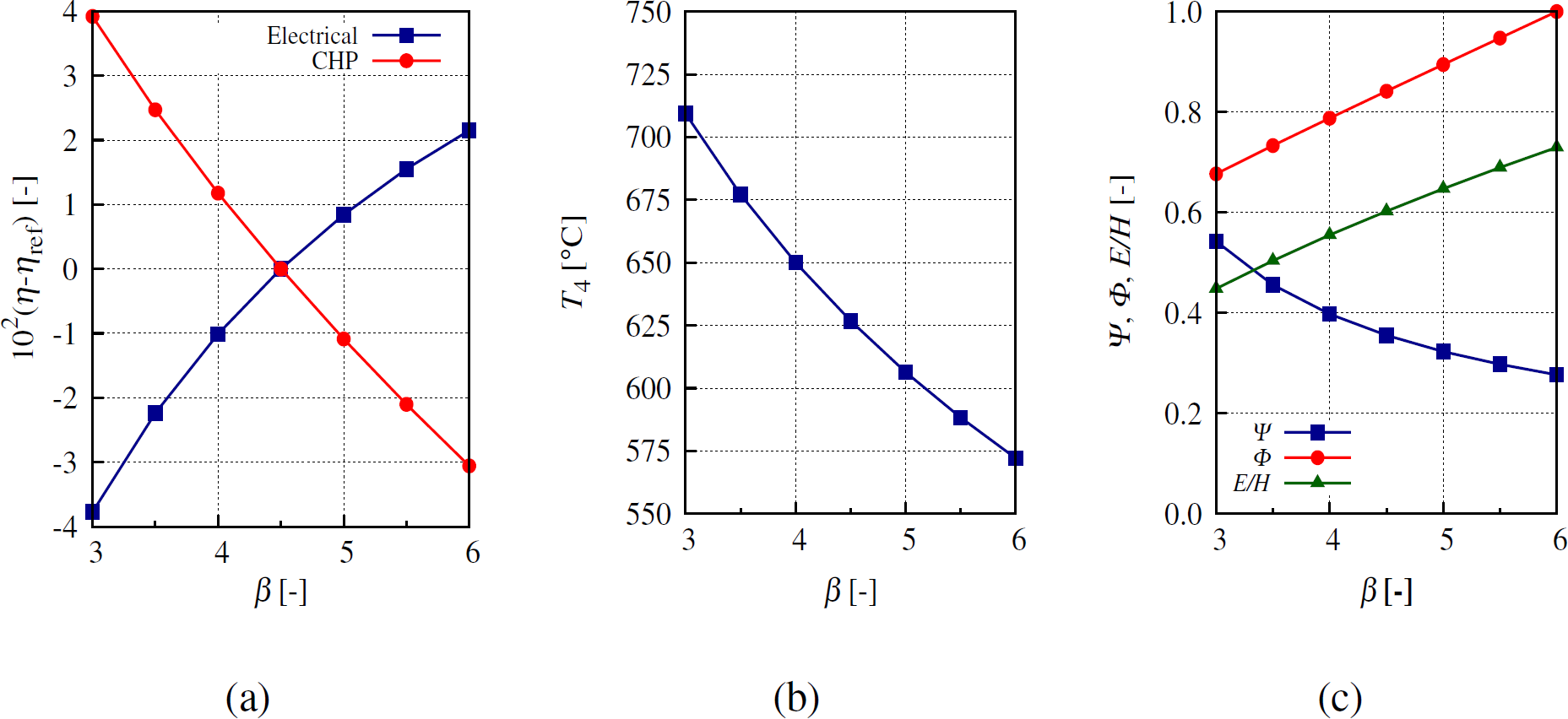
Influence of T5'' on: electrical efficiency and cogeneration efficiency (a), steam turbine outlet (b), and Ψ, ΦS and E/H (c)
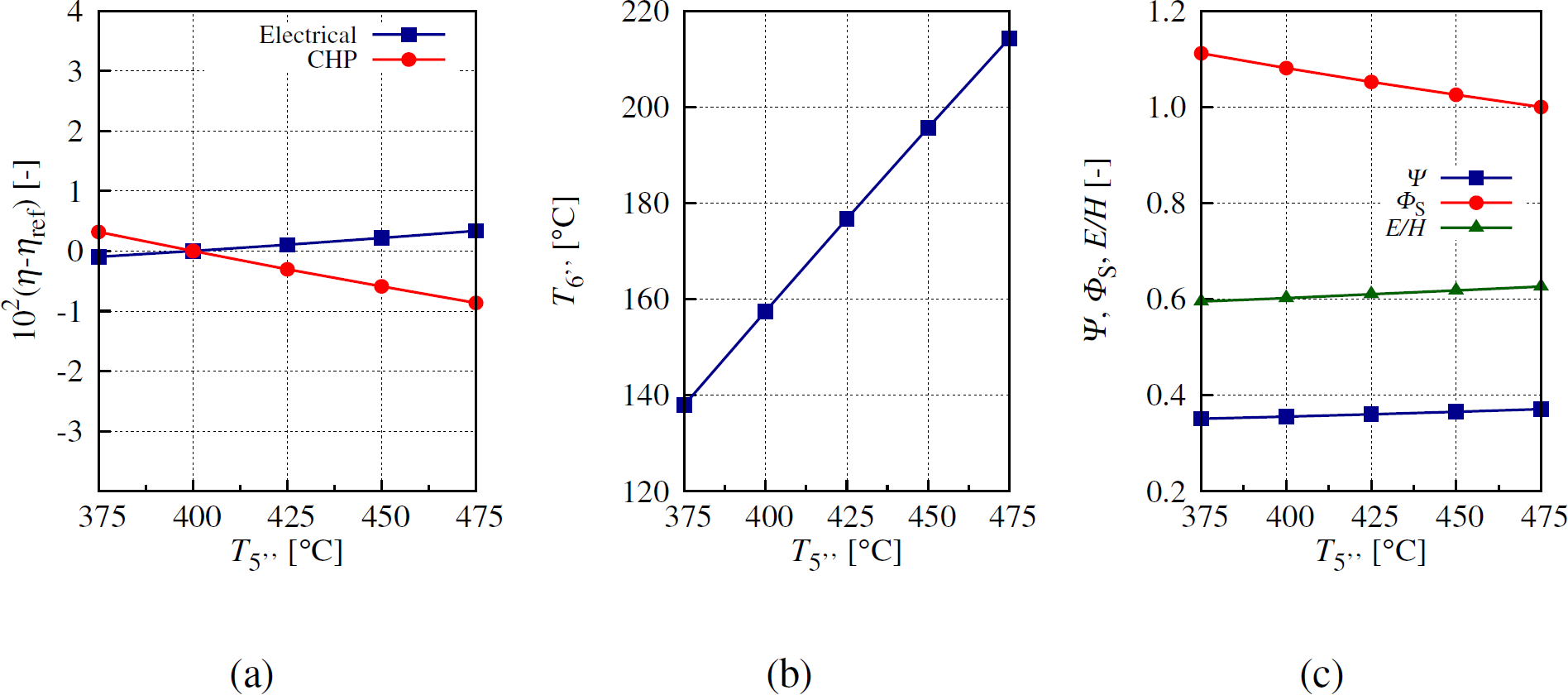
Influence of p5'' on: electrical efficiency and cogeneration efficiency (a), steam turbine outlet (b), and Ψ, ΦS and E/H (c)
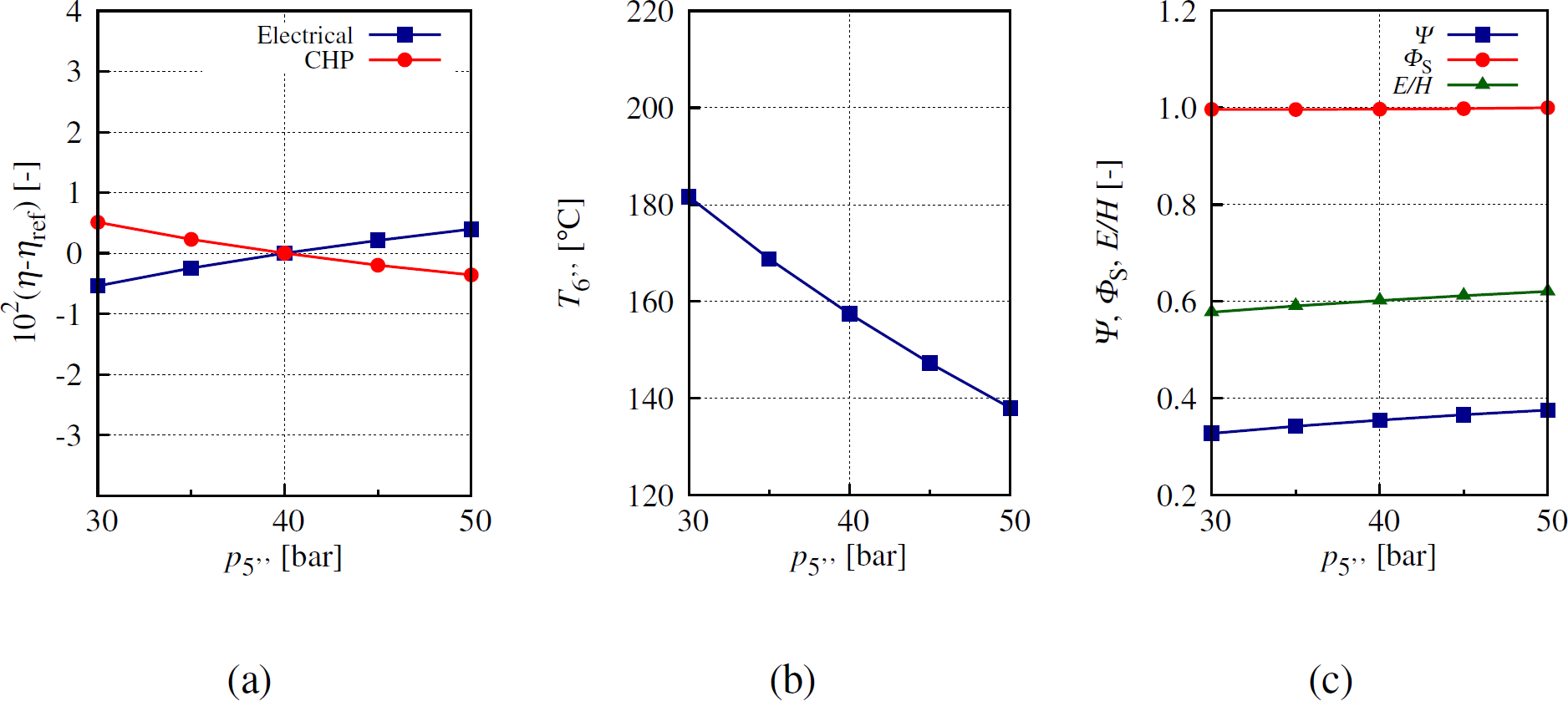
Therefore, a gas turbine pressure ratio of 4.5 and the pressure and temperature values at the steam turbine inlet of 40 bar and 400 °C were respectively identified as good compromises to achieve the aforementioned objectives (high electrical and cogeneration efficiencies and adequate steam production). With these values, we obtain an electrical efficiency of the combined cycle equal to 28.2%, and a cogeneration efficiency equal to 75%. The complete performance of the combined cycle and the main assumptions made are listed in Table 1.
The mini combined cycle described so far can supply an electrical power of about 1.9 MW and a thermal power of about 3.2 MW. Higher energy demands can be met using a series of these mini-modules. In this case, in order to increase the electrical efficiency of the whole plant, it is possible to replace the set of small steam turbines with a single more efficient turbine and also to increase the temperature and pressure of the steam generated in the HRSG. In the case of three mini gas turbines combined with a single 2 MW steam turbine, the proposed plant can produce an electrical power of approximately 6.3 MW and a thermal power of about 8.9 MW, reaching an electrical efficiency of 30.5% and a combined heat and power efficiency of 73.7%.
Evaluated performance and main assumptions
Performance | Assumptions | ||
---|---|---|---|
Mini gas turbine electric power [kW] | 1,436 | Inlet air mass flow rate [kg/s] | 7.54 |
Steam turbine electric power [kW] | 510 | Mini gas turbine intake pressure loss [%] | 1 |
Pump power consumption [kW] | 10 | Isentropic compressor efficiency [%] | 84 |
Combined cycle electrical efficiency [%] | 28.2 | Compressor pressure ratio [-] | 4.5 |
Combined cycle CHP efficiency [%] | 75.0 | Compressor mechanical efficiency [%] | 98 |
Steam mass flow rate [kg/s] | 1.45 | Combustor pressure losses [%] | 3 |
Mini gas turbine exhaust mass flow [kg/s] | 7.68 | TIT [°C] | 950 |
Mini gas turbine exhaust temperature [°C] | 627 | Combustion efficiency [%] | 99 |
Stack temperature [°C] | 178 | Isentropic turbine efficiency [%] | 90.5 |
Steam turbine outlet temperature [°C] | 158 | Turbine mechanical efficiency [%] | 98 |
Mini gas turbine generator efficiency [%] | 94 | ||
Considered LNG composition | HRSG hot side pressure drop [%] | 3 | |
Methane molar content [%] | 97.5 | HRSG thermal losses [%] | 0.7 |
Nitrogen molar content [%] | 0.5 | Sub-cooling temperature difference [°C] | 10 |
Ethane molar content [%] | 1.8 | Economizer cold side pressure drop [%] | 15 |
Propane molar content [%] | 0.2 | Pinch point temperature difference [°C] | 10 |
Calculated LHV [kJ/kg] | 49,504 | Superheater cold side pressure drop [%] | 8 |
Steam turbine admission temperature [°C] | 400 | ||
Ambient conditions | Steam turbine admission pressure [bar] | 40 | |
Ambient temperature [°C] | 15 | Steam turbine outlet pressure [bar] | 3 |
Ambient pressure [bar] | 1.013 | Steam turbine isentropic efficiency [%] | 75.5 |
Ambient humidity [%] | 60 | Pump isentropic efficiency [%] | 83 |
Once the overall characteristics of the mini combined plant are defined, the turbomachines constituting the plant have to be designed. In the following paragraphs, the design procedure adopted to define the mini gas turbine dynamic component geometries, i.e. radial compressor and turbine, is presented. The procedure is based upon the design criteria developed and explained in detail in several papers developed by the authors for lower net power machines: in particular, the overall cycle design is presented in Barsi et al. [11], while the detailed design for turbine and compressor are reported in Perrone et al. [12] and Barsi et al. [13], respectively. In this paper, the main results and overall performance obtained by the procedure, taking into account the scaling criteria analysed in Cumpsty [14], are presented.
The centrifugal compressor and the centripetal turbine first guess geometries, which are required by the optimization procedure, have been designed starting from a one-dimensional preliminary approach aimed at fulfilling the design duty with the best machine efficiency, taking into account mechanical limitations of the materials. In this first design step the main dimensions and blade angles have been found applying 1D equations, starting from statistical relationships and literature data to set the ranges for the main unknown design parameters. Among the others, the literature source was constituted for compressor 1D design mainly by classical texts [14, 15], taking into account, both numerically and experimentally, the rotating effect on radial flow passage [16, 17]. For the turbine 1D design also, classical literature [18, 19] combined with two dimensional approaches [20] have been employed as literature source. For the 1D design, in-house developed codes have been utilized.
In order to achieve functional geometry management during the optimization process, the Numeca/Autoblade software [21] was used. This software allows using an appropriate set of parametric curves for the definition of the meridional channel and of the shape of the blades, using a limited number of parameters while allowing representing a wide range of geometries. In particular, for the definition of the turbine and compressor hub and shroud lines, a composite curve was used consisting of a straight line, a Bezier curve with 4 control points, followed by another straight line. For the parameterization of the compressor rotor blades, controlled in three different spanwise sections, it was decided to use for the camber line, Bezier curves controlled by 5 points equally distributed along the curvilinear coordinate. For the definition of the half-thickness laws of the blades, Bezier curves with 4 control points have been used. The diffuser row is made of straight wedge-shaped blades. Likewise, for the case of the radial turbine, the representation of the impeller blades is similar to that used for the compressor, while the stator row is parameterized using 4-point Bezier curves for both the camber line and the half-thickness laws. Once the limits to the variations of the free parameters and the connection constraints between the different parameters are set, the geometric model of the compressor has 26 degrees of freedom, while for the case of the turbine, the free parameters are 22.
The calculation domain was modelled through Numeca/IGG Autogrid5. For this purpose, a multi-block structured hexahedral mesh was used for each row. About 2 million cells have been used for the radial compressor, while for the centripetal turbine about 1.5 million cells. NumecaFineTurbo code, which solves the Navier Stokes equations, has been used as numerical solver. In particular RANS calculation model [22] coupled with a two-equation Shear Stress Transport (SST) turbulence model to close the problem have been employed. On the solid walls, no-slip condition is applied, and properly set viscous layers are used to allow a value of y+ on the wall next to unity.
Given the high number of geometric variables involved in the parametric model, in order to properly explore the multidimensional domain linked to optimization, a database generated starting from a random sampling equal to 25X and 15X, respectively, for the compressor and for the turbine, has been employed. The optimization procedure is based on the minimization of a single objective function, obtained from the sum, appropriately weighted, of different penalty terms. In particular, for the case of the centrifugal compressor, the objective function has the purpose of maximizing isentropic efficiency, guaranteeing the absolute total pressure ratio of the design and absolute subsonic flow at diffuser inlet. For the case of the radial turbine, on the other hand, the objective function was chosen as the sum of four different terms that respectively guarantee a mass flow equal to the design conditions, maximize the overall efficiency, and control the tangential component of the absolute speed at the impeller outlet within a desired range of values, variable according to the radial coordinate and sampled on 4 spanwise sections.
For the compressor case, the optimization process has reached convergence after about 35 iterations. The meridional channel has been modified: in the optimized case the tip radius of the rotor blade inlet has decreased with respect to the initial configuration. This entails a reduction of the relative Mach number corresponding to the impeller inlet at tip, which passes from 1.35 of the original case to 1.2 in the optimized case, and leading to a significant reduction of the relative supersonic flow within the entire impeller. Also the blade thickness at leading edge is reduced, that in turns leads to a reduction in the intensity of the shock wave within the blade channel, even if the greatest contribution to the reduction of this intensity is linked to the null value of the curvature of the blade at leading edge. Moreover, in the optimized configuration, due to an increase in the backswept angle of the rotor blade, the absolute velocity at the impeller outlet decreases, consequently leading to a decrease in the absolute Mach number inside the diffuser. The main overall performance is summarized in Table 2.
Original and optimized overall performance for radial compressor
Original | Optimized | |
---|---|---|
ṁ [kg/s] | 7.6 | 7.6 |
η [-] | 0.80 | 0.84 |
Inlet relative Mach at impeller tip [-] | 1.35 | 1.2 |
Absolute Mach at diffuser inlet [-] | 1.4 | 0.98 |
For the turbine case, the optimization process required about 30 iterations to achieve convergence. The procedure allowed modifying the blade geometry obtaining a reduction in the rotor incidence angle. This result is obtained by increasing the tangential component of the absolute velocity at the stator outlet, in turn obtained by reducing the height of the channel (Figure 5) and increasing the angle of the absolute flow at stator outlet. The restoration of the correct incidence on the rotor blade leads to a better load of the blade. The increase of the tangential component of the absolute velocity at the stator outlet leads to an increase in the absolute Mach number in this zone, which, however, remains below the unity.
Original (red) and optimized (black) meridional channel configurations
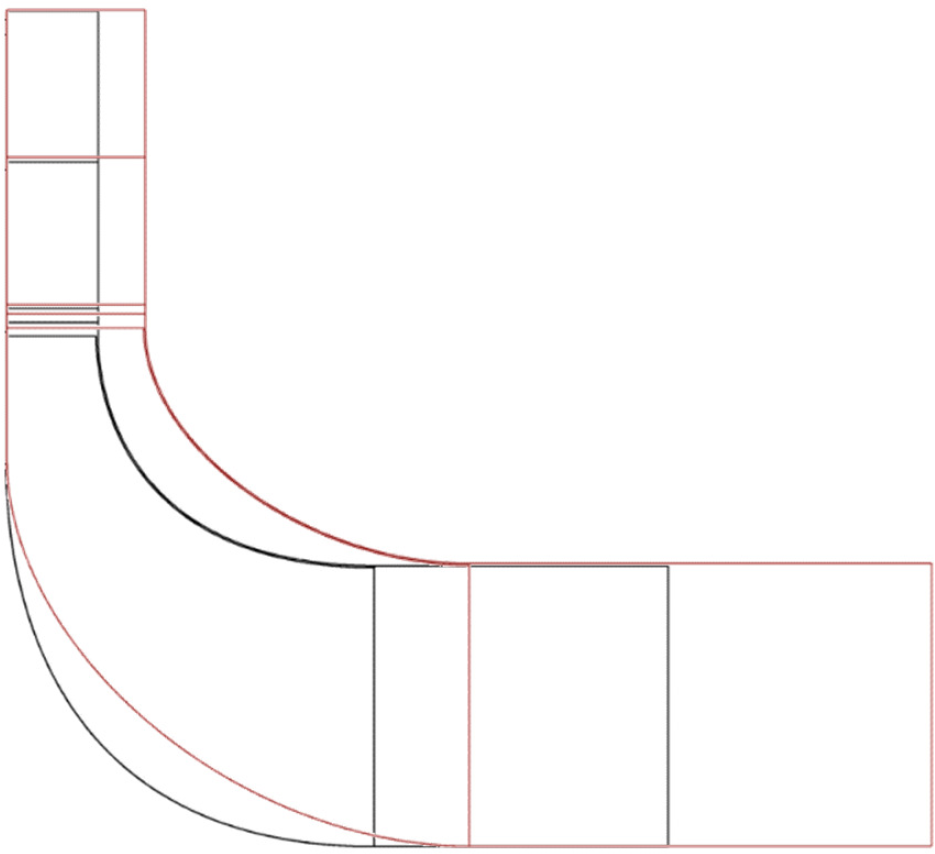
The original and optimized overall performance are summarized in Table 3.
Original and optimized overall performance for radial inflow turbine
Original | Optimized | |
---|---|---|
ṁ [kg/s] | 7.7 | 7.7 |
η [-] | 0.872 | 0.905 |
The mini cogeneration combined cycle design, as described in the previous sections, provides the optimal values of the parameters that are significant for sizing the turbomachines involved in the cycle, values which depend on the cogeneration cycle configuration adopted to comply with different power demands. Specifically, the inlet steam conditions for the steam turbine are defined by pressure and temperature conditions of 40 bar and 400 °C. The inlet steam conditions, together with the exhaust steam pressure and steam flow rate for the required power output summarized in Table 4, represent the boundary conditions for the design of the steam turbine. The data reported in Table 4 allow the preliminary choice of the machine model. Fincantieri S.p.A. has developed a machine type, which is especially suited for the kind of applications considered in the present paper: it is a compact size multi-stage, multi-valve impulse type steam turbine, that can be configured both for condensing and for backpressure applications, optionally with bleeding or second admission flows. The turbine is packaged on a single metallic baseplate with rotational speed reduction gear, electric generator, lube oil console and control panels, in order to reduce the installation time. This type of steam turbine can accept inlet steam conditions ranging from 10 bar to 60 bar of pressure and from saturated steam temperature to 450 °C for superheated steam. The steam can be exhausted at a pressure level ranging from 0.05 bar to 10 bar. The shaft speed for the application is up to 19,000 rpm, with a supplied electrical power output ranging from 100 kW to 2,000 kW. The wide range of inlet and outlet steam conditions and the flexibility provided by the modular layout allow this type of turbine to be considered in a wide range of applications such as combined cycle both on terrestrial and naval applications, waste energy recovery, industrial energy recovery, process plants that use steam for the production process, where it is possible to install a small turbine for energy production and obtain steam for the process from bleed or turbine exhaust.
Steam turbine main design parameters
Design data | ||||
---|---|---|---|---|
Inlet pressure [bar] | Inlet temperature [°C] | Exhaust pressure [bar] | Approx. mass flow rate [kg/h] | |
500 kW | 40 | 400 | 3 | 5,220 |
The steam turbine size has been defined and developed by Fincantieri S.p.A. based on indication of market trends that highlight a growing demand for small power units. The steam turbine and its auxiliary components therefore will be of small footprint layout, and are provided as a pre-assembled product on a single skid. Due to the compact dimension and small blade mean diameter, of about 240 mm, the rotational speed is increased up to 19,000 rpm in order to maintain a high efficiency level. The small diameter of application of the flow path aerodynamic components therefore imply a significant three-dimensionality and spanwise variation of the distribution of thermodynamic parameters, and consequently the need to address the blades design accounting for these effects with proper engineering tools and design effort. The internal components of the flow path are developed by means of both proprietary and commercial codes, with increasing level of complexity of flow modelling from 1D meanline analysis to a complete 3D CFD viscous analysis to perform detailed flow field optimization. The development of new aerodynamic profiles is carried out by means of repeated Computational Fluid Dynamics (CFD) analyses performed with Numeca commercial code FINE/Turbo. This code is also used to perform specific 3D analyses in case further studies of the details of complex flows in particular conditions of operation are needed. During the blade profile design phase, experimental tests on aerodynamic components can be performed in case they are needed to support the design activity and validate results from the detailed analyses described above. The challenge to obtain a high level of efficiency in case of turbines of small dimension is also addressed with the reduction of leakage flows aimed to achieve high volumetric efficiency. This improvement is obtained with specific design for the labyrinth seals, which includes the adoption of brush devices to minimize the leakage flow. The design procedure is of course completed with all the necessary structural and vibrational assessment of the rotor and of the bladed components by means of both proprietary software modules and commercial Finite Element Analysis (FEA) programs. Machines designed according to the aforementioned procedure typically achieve internal efficiency levels ranging between 76% and 82% for compact design and output power comparable to those studied in the present paper. The 3D CAD models are directly used in the production phase for the manufacturing process and final quality testing. The steam turbine generator and its auxiliary systems are finally assembled on a single “plug and play” skid, for ease of transport and installation. For the specific application described in the present work, the same approach to a simple and functional layout will be applied to the combined gas and steam turbine installation. Moreover, as part of the standard design and production procedure, the final product is normally verified and tested in the facility located in Fincantieri S.p.A. production site.
In this work the architecture of a small-scale combined cycle plant was defined, consisting of a mini gas turbine and a steam turbine capable of supplying both electrical power and heat in the form of steam, for naval applications. In order to achieve the goal of contemporarily obtaining a good electrical and cogeneration efficiencies, and guaranteeing an adequate production of low pressure steam, a cycle optimization analysis was made in order to first establish the repartition of electrical power between the top and the bottom cycle. The performance of the combined cycle was evaluated through the GE GateCycle® simulation software. The values of pressure ratio and thermodynamic conditions at the entrance of the steam turbine were changed within the admitted ranges to the aim of identifying a good compromise between the need to obtain a good electrical efficiency and a high cogeneration efficiency. This analysis led to adopt a GT of about 1.4 MW and a ST of about 0.5 MW, with a GT pressure ratio of 4.5 and pressure and temperature values at the steam turbine inlet of 40 bar (abs) and 400 °C, respectively. With these values an electrical efficiency of the combined cycle equal to 28.2%, and a cogeneration efficiency equal to 75% have been obtained, providing an electrical power of about 1.9 MW and a thermal power of about 3.2 MW. Starting from the cycle optimization results, the single turbomachines for both topping and bottoming cycles have been designed, and the fundamental design steps have been described.
The amount of electrical and thermal power provided by the innovative mini-cycle, and its compactness make it particularly appealing not only as prime mover for small vessels or auxiliary engine for larger vessels, but also for off-shore or terrestrial cogenerative applications.
E | electric power | [kW] |
h | specific enthalpy | [J/kg] |
H | thermal power | [kW] |
ṁ | mass flow rate | [kg/s] |
Ma | Mach number | [-] |
p | pressure | [Pa] |
s | specific entropy | [J/kgK] |
T | temperature | [K] |
y+ | dimensionless wall distance | [-] |
Greek letters | ||
β | pressure ratio | [-] |
η | efficiency | [-] |
ηref | reference efficiency, obtained for β = 4.5, p5’’ = 40 bar, T5’’ = 400 °C | [-] |
η | machine isentropic efficiency | [-] |
Φ | exhaust mass flow rate made non dimensional by the exhaust mass flow rate at the maximum pressure ratio | [-] |
ΦS | steam mass flow rate made non dimensional by the steam mass flow rate generated at the maximum temperature | [-] |
ψ | steam turbine to gas turbine power ratio | [-] |
Abbreviations | ||
CHP | Combined Heat and Power | |
COGES | Combined Gas Turbine Electric and Steam | |
GT | Gas Turbine | |
HFO | Heavy Fuel Oil | |
HRSG | Heat Recovery Steam Generator | |
IMO | International Maritime Organization | |
LNG | Liquefied Natural Gas | |
RANS | Reynolds Averaged Navier Stokes | |
ST | Steam Turbine | |
UHC | Unburned Hydro Carbons |
Comparing Combined Gas Turbine/Steam Turbine and Marine Low Speed Piston Engine/Steam Turbine Systems in Naval Applications ,Polish Maritime Research , Vol. 18 (4),pp 43-48 , 2011, https://doi.org/https://doi.org/10.2478/v10012-011-0025-8
, Comparison Between Natural Gas and Diesel Fuel Oil Onboard Gas Turbine Powered Ships ,JKAU: Mar. Sci. , Vol. 23 (2),pp 109-127 , 2012, https://doi.org/https://doi.org/10.4197/Mar.23-2.7
, Pioneering Gas Turbine-Electric System in Cruise Ships: A Performance Update ,Marine Technology , Vol. 41 (4),pp 161-166 , 2004
, A Review on the Use of Gas and Steam Turbine Combined Cycles as Prime Movers for Large Ships. Part I: Background and Design ,Energy Convers. Manag. , Vol. 49 (12),pp 3458-3467 , 2008, https://doi.org/https://doi.org/10.1016/j.enconman.2008.08.005
, A Review on the Use of Gas and Steam Turbine Combined Cycles as Prime Movers for Large Ships. Part II: Previous Work and Implications ,Energy Convers. Manag. , Vol. 49 (12),pp 3468-3475 , 2008, https://doi.org/https://doi.org/10.1016/j.enconman.2008.08.004
, A Review on the Use of Gas and Steam Turbine Combined Cycles as Prime Movers for Large Ships. Part III: Fuels and Emissions ,Energy Convers. Manag. , Vol. 49 (12),pp 3476-3482 , 2008, https://doi.org/https://doi.org/10.1016/j.enconman.2008.08.003
, Economic Analysis of Small Size Gas Turbine Based CHP Plants in the Present Italian Context ,International Journal of Heat and Technology , Vol. 34 (2),pp 443-450 , 2016, https://doi.org/https://doi.org/10.18280/ijht.34Sp0236
, - , US Patent 8,640,437, 2014
- GE Enter Software for Windows Version, 2005, www.gepower.com
Compressor and Turbine Multidisciplinary Design for Highly Efficient Micro-gas Turbine ,Journal of Thermal Science , Vol. 27 (3),pp 259-269 , 2018, https://doi.org/https://doi.org/10.1007/s11630-018-1007-2
, - , Radial Inflow Turbine Design Through Multidisciplinary Optimization Technique, Proceedings of the ASME Turbo Expo 2015: Turbine Technical Conference and Exposition GT2015, 2015
- , Multi-Disciplinary Optimization of a Centrifugal Compressor for Micro-Turbine Applications, Proceedings of the ASME Turbo Expo 2016: Turbine Technical Conference and Exposition GT2016, 2016
Design of a Centrifugal Compressor for Micro Gas Turbine: Investigation of Scaling and Tip Clearance Effects ,Open Journal of Fluid Dynamics , Vol. 9 (1),pp 49-62 , 2019, https://doi.org/https://doi.org/10.4236/ojfd.2019.91003
, - , Longman Scientific & Technical, Compressor Aerodynamics, 1989
Swirling Impeller Flow ,Journal of Turbomachinery , Vol. 110 (1),pp 122-128 , 1988, https://doi.org/https://doi.org/10.1115/1.3262157
, A Wake and an Eddy in a Rotating, Radial-Flow Passage ‒ Part 1: Experimental Observations (and Part 2: Flow Model) ,Journal of Engineering for Power , Vol. 95 (3),pp 205-219 , 1973, https://doi.org/https://doi.org/10.1115/1.3445724
, - , An Optimization Technique for Radial Compressor Impellers, Proceedings of the ASME Turbo Expo, 2008
- , Longman, Design of Radial Turbomachines, 1990
- , Radial-inflow Turbines, Turbine Design and Application, 1975
- , The Application of Throughflow Optimisation to the Design of Radial and Mixed Flow Turbines, Proceedings of the 9th International Conference on Turbochargers and Turbocharging, 2010
- , User Manuals, Academic R&D License, 2018
A Multiblock/Multigrid Code for the Efficient Solution of Complex 3D Navier-Stokes Flows ,Aerothermodynamics for Space Vehicles ,pp 415-420 , 1991
,